Control valves must be selected for their intended application, and advantages must be weighed against limitations to ensure that the correct valve is selected. Different valve types are suited to perform different duties while valve characteristics, including fluid flow, shut off, and noise, can be manipulated by choosing specific valve components. When installing a control valve in a location where it may encounter extreme conditions, such as cryogenic temperatures or high differential pressures, proper valve assemblies should be specified to handle anticipated conditions.
The type of control valve chosen for a specific application will depend on the anticipated conditions and service. For instance, when slurry or entrapped solids are expected to flow through a control valve, a knife-type gate valve can be used, due to its ability to slice through foreign objects in the fluid, and thereby offer tight shut-off. While knife-type gate valves offer good sealing capabilities, they would not fare quite as well when called upon to throttle that flow due to the inherent vibration of the gate at partially open conditions. Advantages and disadvantages of each type of valve must be considered to select the proper type for the intended application.
Control valve components are also selected due to the effect they have on flow through the valve. For example, the noise characteristics of a valve can be modified by replacing or removing the cage component within the valve. Replacing the cage can also have a large effect on flow characteristics through the valve, and can even play a role in causing or preventing pump cavitation. Simple plug valves, which do not include a cage component, do this with differing plug designs or shapes.
Extreme operating conditions will necessitate the use of specific valve components and/or types of valves. Extremely high or low fluid temperatures could potentially damage the valve packing and cause leaks; therefore, an extended bonnet design may be beneficial by allowing the packing material to be placed further away from the process flow. High differential pressure across a valve is another situation that may require special consideration. At high differential pressures, single seat valves have a tendency to slam closed while at low flow conditions. In this situation, a balanced-plug cage guided valve could be substituted, which, by its internal design, nullifies the pressure differential across the valve, saving money on larger than necessary actuator costs.
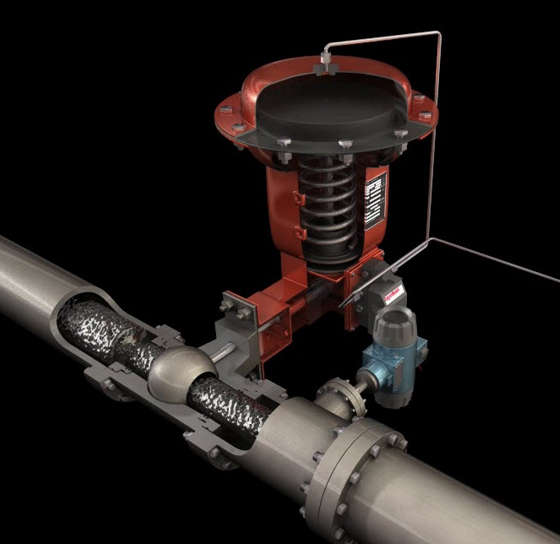
Control Valve Selection
Control valves come in a variety of types, configurations, and with a multitude of accessories. Selecting a control valve for your specific applications can become a daunting task, especially when one considers the possible consequences of poor choices, including immediate failures and long term inefficient operation, both of which could lead to large cost overruns and affect productivity.